When constructing any type of façade for any purpose, protecting it with the right passive fire protection solutions is crucial. However, even the most robust and carefully considered fire safety specification can underperform if not installed correctly, undermining the overarching fire safety strategy and increasing the risk to life and property.
Installation Quality
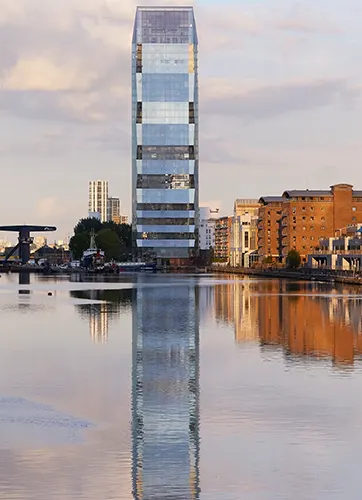
Passive fire protection is built into the building envelope and works by containing the spread of fire, heat, and smoke by creating areas of manageable risk— known as compartments— using fire-resistant materials and gap-filling measures. This limits the movement of flames and smoke, protecting escape routes and reducing the risk of fire-induced structural damage which could result in collapse. Whilst these solutions do not need any input from the building owners or operators, they must be installed correctly to work as intended. Failure to do so could result in gaps in the compartment. This could be caused by inadequate fire-stopping around penetrations such as pipes or gaps, or openings forming between fire-resistant elements such as between the floor slab and the wall construction. These breaches could then provide an easy path for flames, heat, and smoke to spread up and around the building in the event of a fire.
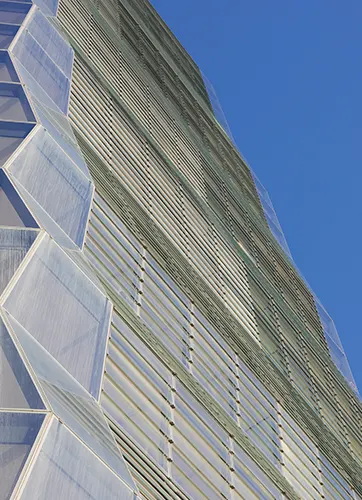
properly to contain fire and smoke spread
Additionally, passive fire protection solutions that are not installed in line with their manufacturer’s recommendations may not achieve the project’s fire safety design requirement. This is because the installation will not be reflective of the way the products have been designed to work and tested to demonstrate how they would perform. Issues could include the use of incorrect fixings, installing products in the wrong orientation or without the right level of compression, and using them alongside other passive fire protection solutions in untested ways. This could result in a solution that underperforms, reducing the time it will resist fire spread from one compartment to another.
Products Selection

with ease of installation in mind – form, fit
and function
With mitigating the risk of human error in mind, using products that have been engineered to be installed quickly and easily can assist in meeting a project’s design intent. This can not only help to ensure a safer project but can help to reduce additional costs and lost time associated with remedial works. For example, the vertical fibre orientation of dry-fix Lamella fire-stopping products, coupled with clear instructions on the foil facings, can help guide the installer in the correct direction in which to install.
Add it with listing requirements for third-party certified tested systems, some curtain wall fire-stopping products carry standardized compression percentages of 10, 12, or 20% for voids of varying sizes, which can simplify the calculation for the installer onsite. This differs from two-part, wet-fix fire-stopping solutions, where the compression requirement for the insulation ‘safing’ component can jump anywhere from 25% to 33% and 55% depending on the listing requirement, and if different safing products from different manufacturers are used interchangeably, the passive fire safety of a project can be compromised.
Factory-engineered one-part solutions not only reduce complications commonly associated with traditional safing material such as: calculating compression; cutting to different dimensions; having to install different sized sections in multiple layers before the wet-apply smoke seal is applied; and dealing with challenges presented by curved and inclined facades, but their dry-fix application also makes it easier to judge the bracket location and distance and ensure tight jointing.
Inspection
Another key benefit of dry-fix fire-stopping products is that there is no need for destructive inspection to sign off their installation, with visual inspections being sufficient. Where required or desired, some manufacturers can also provide these inspections to verify whether their fire-stopping and cavity barrier products and systems have been correctly installed. This can be invaluable, particularly on large and complex buildings where there may be many different considerations.
Whilst some projects may need or prefer an in-person inspection, some manufacturers also offer inspection apps to streamline this process for contractors working onsite as well as for façade consultants wanting to check the progress and quality of the installation. Typically, only suitable for standard systems, they can allow users to capture images as each area/element is installed and update the data input fields using their smartphone or tablet. The app then immediately turns this into a comprehensive report which can be reviewed offsite by a technical team to ensure the installation meets recommendations and quickly identify if any areas need remedial actions.
Competency and Training
Of course, making sure installers are equipped with all the necessary knowledge to deliver an effective installation is important. Working with manufacturers who provide practical onsite training that includes everything from ‘toolbox talks’ to ensure installation instructions and method statements are understood, to delivering practical training and benchmark installations, can provide installers with invaluable insight into potential practical challenges, allowing them to be addressed before the install has progressed.
Moreover, unless a specialist façade contractor with dedicated firestop and cavity barrier installers has been appointed, the individuals installing the safing measures can change from project to project, or even at different stages of a single project. Therefore, having access to manufacturer training throughout the project, and not just at the start, can help to ensure continual adherence to the fire safety strategy.
For this training and onsite support to be effective, early engagement with the product manufacturer is crucial. This is especially true for ambitious, complex designs that need a tailored installation approach, or where there are deviations from the original drawings due to unforeseen challenges or changes in conditions onsite. Additionally, manufacturers can often feedback to design teams so they can learn to help improve the practicality of future designs, ensuring continuous improvement and collaboration.
Hidden Defence
Installation is crucial to the effectiveness of passive fire protection solutions. Therefore, it is vital installers on all kinds of projects feel confident and competent to deliver accuracy on site. Engaging with manufacturers as early as possible in the process can provide the support necessary to ensure products are handled and fitted in line with recommendations and that they will perform as expected in the unfortunate event of a fire.
(For more information, please email: siderisein@siderise.com or visit www. siderise.com)